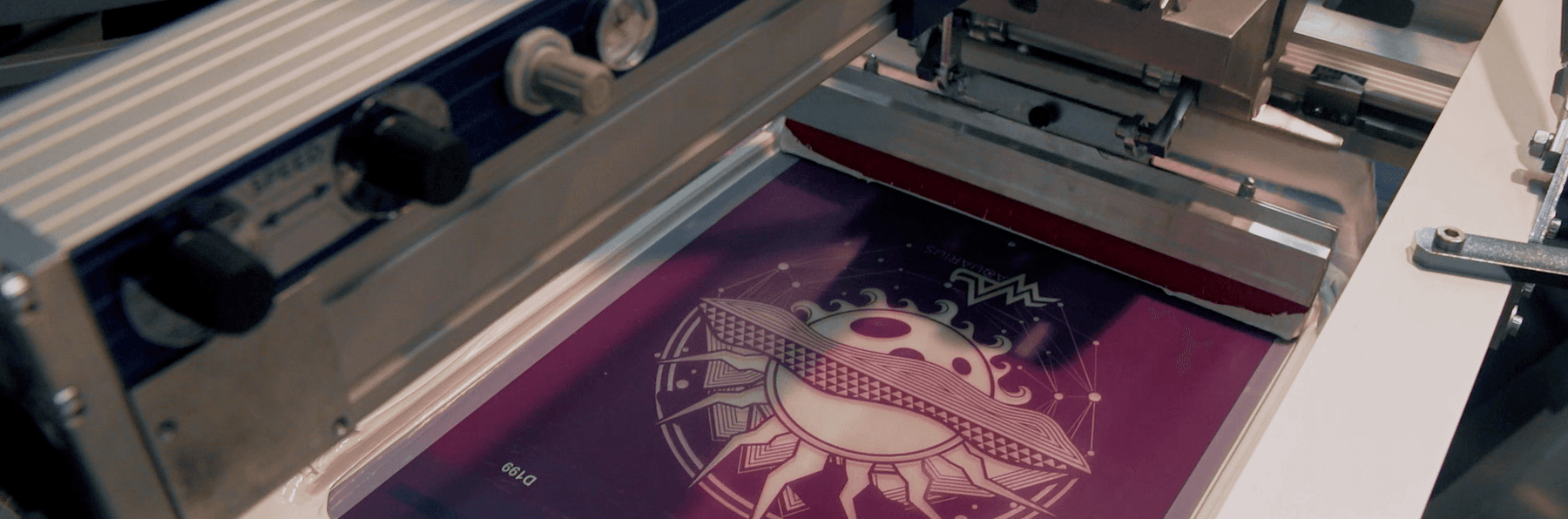
The Dark Art of Discharge Printing.
The screen printing industry is in constant change and there are a multitude of ways to print onto t-shirts.
It takes most of us long enough to master the art of pushing sticky plastisol ink through a mesh, and yet our customers are always striving for that novel new technique that they believe you are automatically a zen master of.
Discharge is a yucky sounding word that despite its hints of sounding like a medical condition that you would not talk about in public, is a technique that uses the ink technology to replace or discharge the color of the shirt with the pigment in the ink, replacing the need for a white primer layer. This should make our lives as printers easy right?
As usual it is not quite as straight forward as to replace the need for an under base permanently, that would be far too easy. The ink technology requires pre-determined conditions to allow the ink to work its magic.
The substrate must be organic, and during the early introduction of discharge this was a plus point, as it worked fantastically well on heavy premium grade cotton fabric, it leaves almost no feel or hand on the garment and this contributed to the high value, fashion based products that made the technique so popular, but this left out a significant market in the performance wear sector.
Discharge has a small amount of formaldehyde in its composition; therefore, it is not recommended for youths’ garments, it is recommended to launder all garments printed with discharge inks before wearing.
The ink system is a water-based system that uses a binder or clear carrier base to which colored pigments are added.
An activator is added prior to production, it is important to note that as soon as this additive is added, the ink starts to degrade and the magic enchantment gives a pot life of around 8 hours starts to tick down. The fact that the activated ink must be thrown away after a shift is another complication that must be managed, combine this with the fact that the colour opacity of the ink is affected by the garment composition and we are starting to see that discharge is not quite the easy option we thought it might be.
Ink mixed with 6% red pigment loaded into clear carrier and an addition of 6% activator is cheaper than most plastisols and is much more environmentally friendly in the clean up process, when printed directly onto the black cotton garment it looks like a major disaster has happened! The ink has no opacity, looks remarkably like a brown stain that the name lends itself to, and we are left scratching our heads wondering where we went wrong!
Then the ink passes through the dryer, the chemicals start to whisper long lost Latin spells and dark forces that have laid dormant for millennia work their shadowy powers on the cotton fibres, transforming them back through the tunnels of time to an era before they were coloured with a sulphurous concoction of dyes, ok maybe I got carried away, the heat causes the ink to remove or bleach away the colour of the cotton and the red pigment sits nice and bright on the now ecru coloured bleached cotton, looking like a freshly painted post box and with no perceptible feel, the holy grail of bright opaque printing.
The ability to remove the dye of the shirt in the specific area where we want to print does sound like a magical solution to the problem of using an underbase, some of the downsides including the short pot life, the unpredictable color strength and the time consuming clean up techniques involved in multi-color jobs have led to a technique which combines the ease and certainty of plastisol and the enchanting properties of discharge, printers are printing a discharge base and flashing it, then dropping on top through fine (90t) mesh counts, good old reliable and opaque plastisol, the resulting print is bright, has a significantly reduced hand and is faster to clean up at the end of a shift, only one screen needs washing thoroughly with water, and only one colour is wasted when the pot life has been reached.
The introduction of new HSA (High Solids Acrylic) inks may be the sounding of the death knell for discharge inks as they give us the opacity we crave and they tick all the green eco friendly boxes. They give us soft feel prints onto 100% polyester performance wear, they don’t have a limited pot life and require no activator, they lack the Dark Mystical powers of discharge, but maybe its time we embraced the science of the future and moved away from the dark art of discharge.
Article written by Tony Palmer, Palmprint
Tony has more than 30 years experience in garment decoration ranging from manual screen printing on hand carousels to the operation of multi-color automatic presses. Specifically Tony is an expert on MHM Automatics, Tesoma, Exile Spyder, Douthitt CTS, Zentner, and numerous manufacturers of textile decorating equipment.
#spsiinc #palmprint #mhmscreenprinting